Cement is the main ingredient in concrete – the second most consumed material in the world (after water) and the foundation of our communities across the globe. Cement producers are constantly pursuing innovative, efficient, and environmentally responsible ways of producing high-quality cement to realize carbon neutrality across the concrete value chain by 2050. Take a look at how cement, the main ingredient of concrete, is made.
Sustainably Producing Cement
Step 1
Quarrying the raw materials
Step 2
The primary crusher
Step 3
Grinding and blending
Step 4
The preheater tower
Step 5A
The materials enter the kiln
Step 5B
The formation of clinker
Step 6
Clinker is cooled for use
The bag house
Step 7
The ball mill
Step 8
Ready for construction
Sustainably Producing Cement
Cement is the main ingredient in concrete – the second most consumed material in the world (after water) and the foundation of our communities across the globe. Cement producers are constantly pursuing innovative, efficient, and environmentally responsible ways of producing high-quality cement to realize carbon neutrality across the concrete value chain by 2050. Take a look at how cement, the main ingredient of concrete, is made.
Swipe to learn about each step



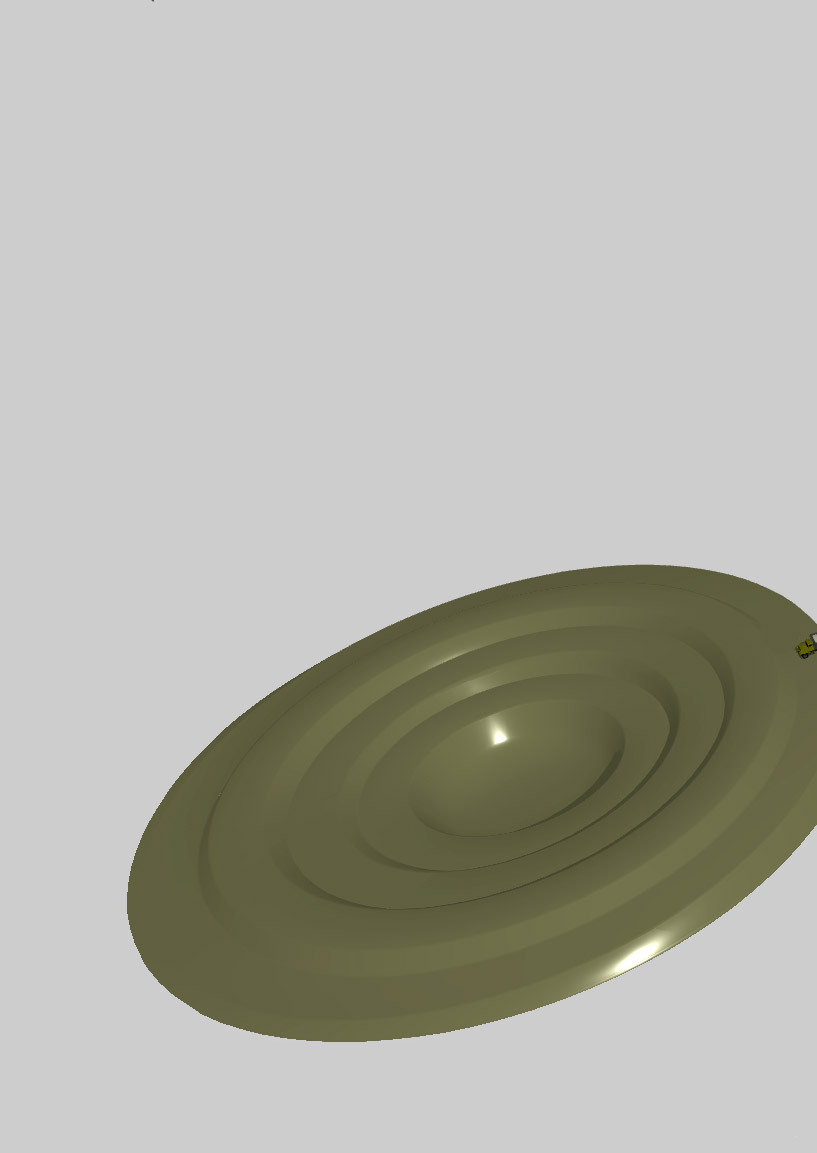
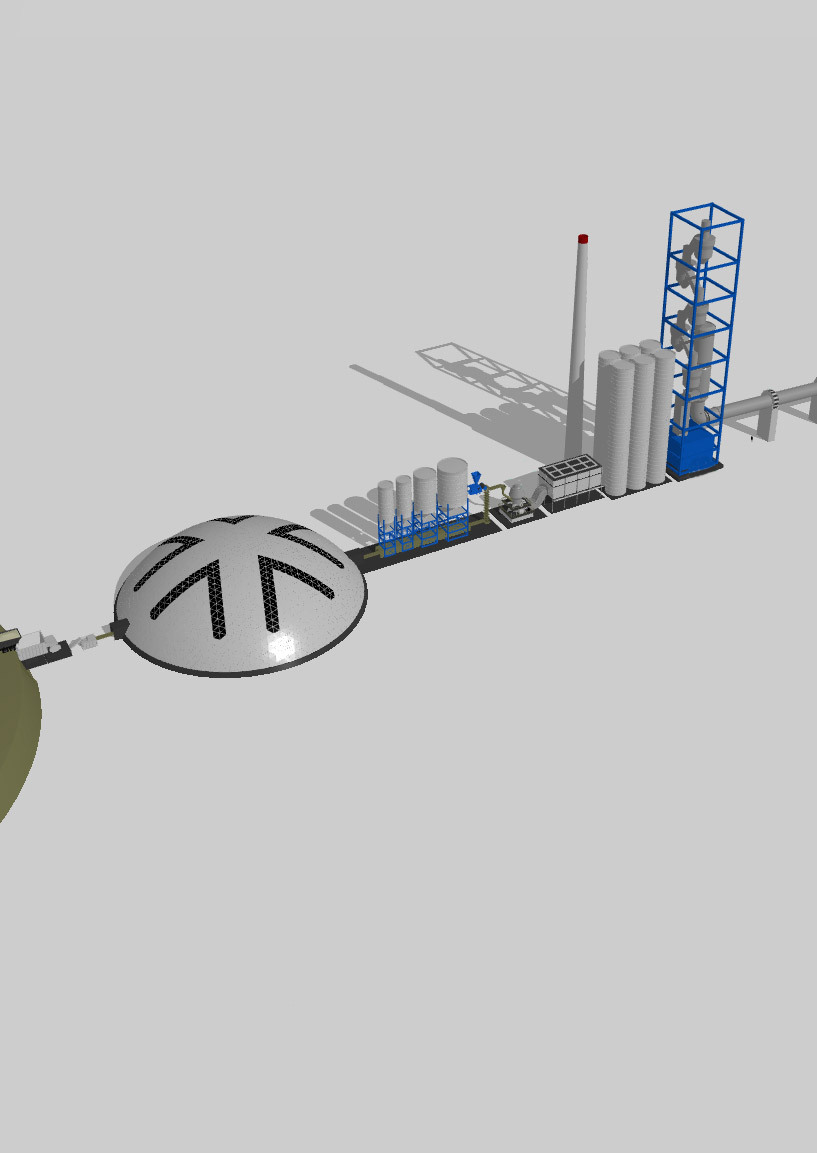
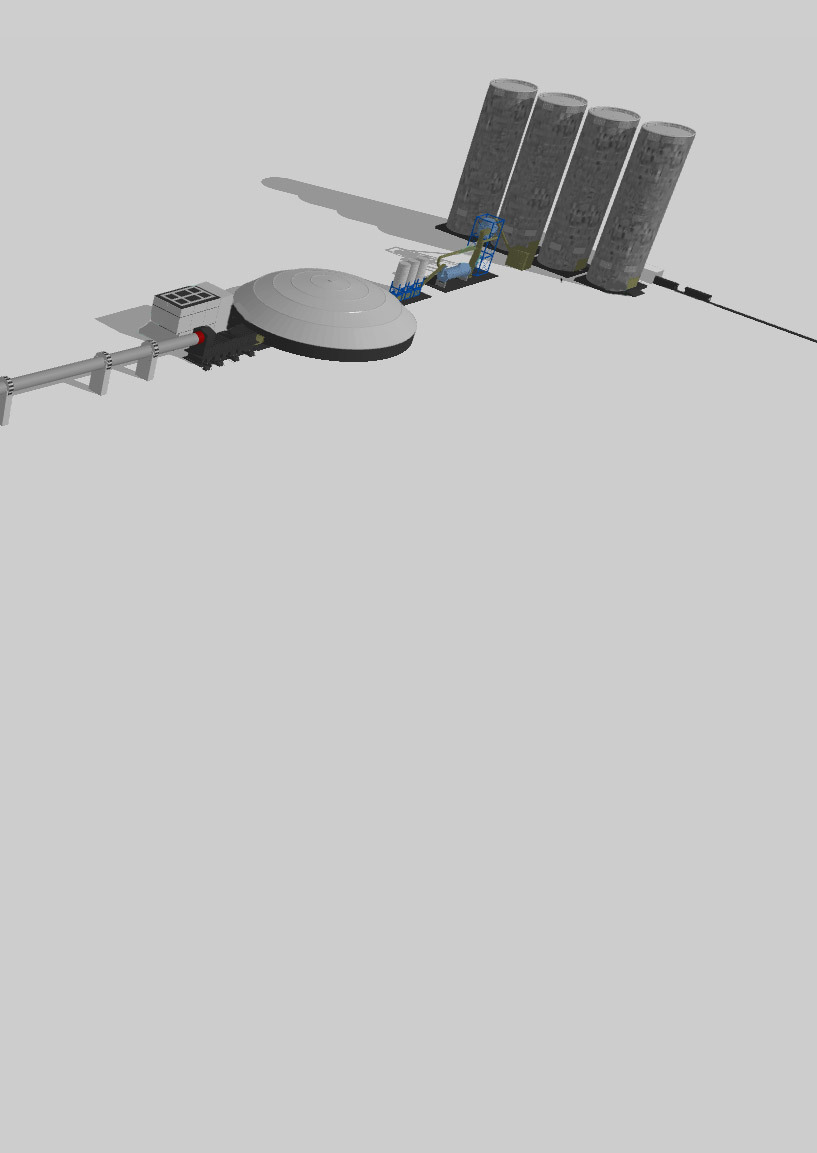
Quarrying the raw materials
The first step is to quarry the raw materials necessary to make cement, which is mainly limestone coupled with clay and sand. Using fly ash or other byproducts to partially replace the raw materials keeps things like fly ash and industrial byproducts out of landfills and contributes to a circular economy.
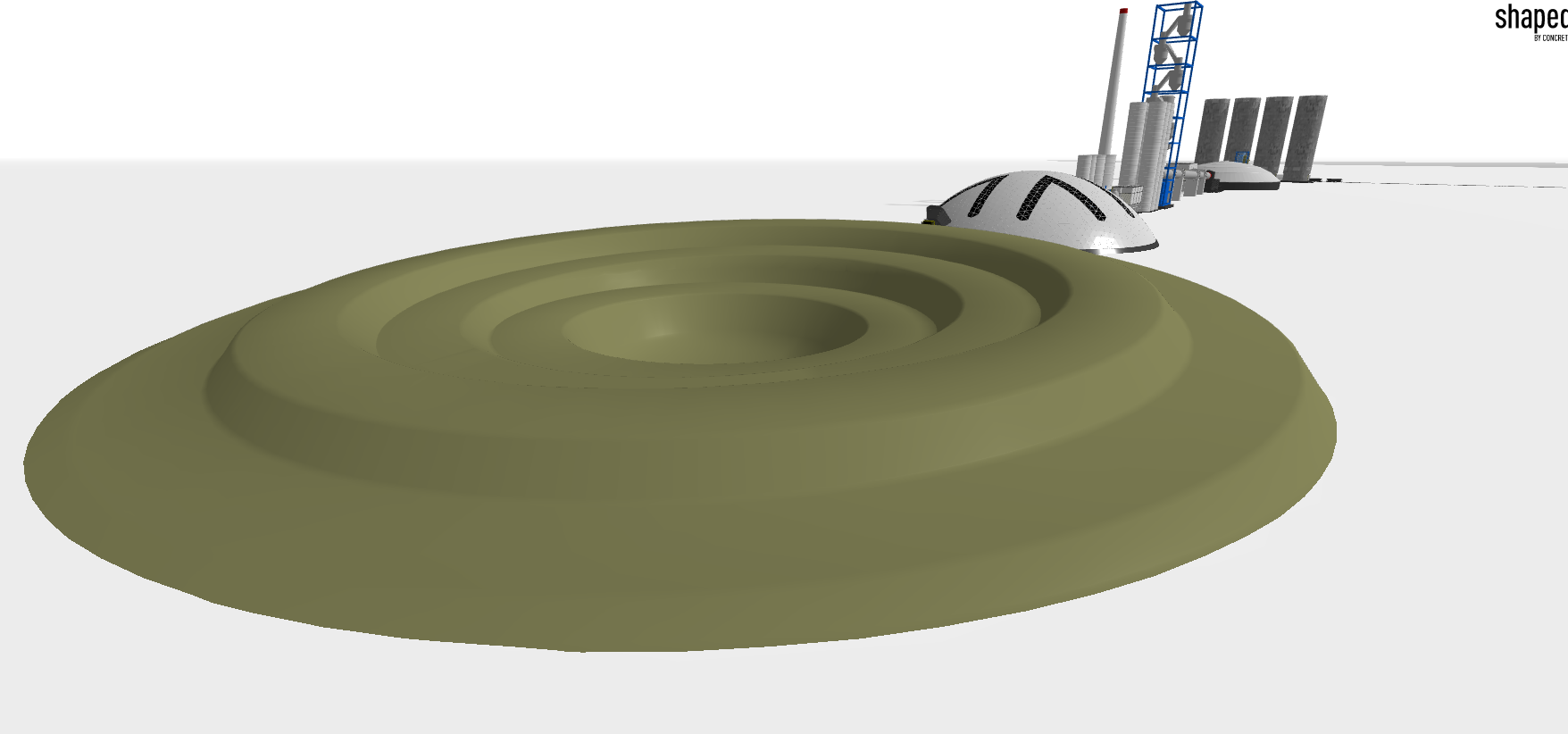
The primary crusher
After quarrying the rock, it is crushed into baseball sized pieces. Once crushed, the raw materials are then sent to a laboratory and analyzed – each step of the cement production process is carefully monitored to ensure efficiency and quality.

Mixing, grinding, and blending the ingredients
The crushed rock is then ground finer (in this case, in a vertical roller mill) and combined with other ingredients. Common materials used to manufacture cement include limestone, chalk, and marl combined with shale, clay, slate, blast-furnace slag, silica sand, and iron ore. Numerous industrial byproducts are used to supplement some or all of these components. Examples of recycled materials that are used include spent pot liners, slags, fly ash or bottom ashes, and various incinerator ashes.
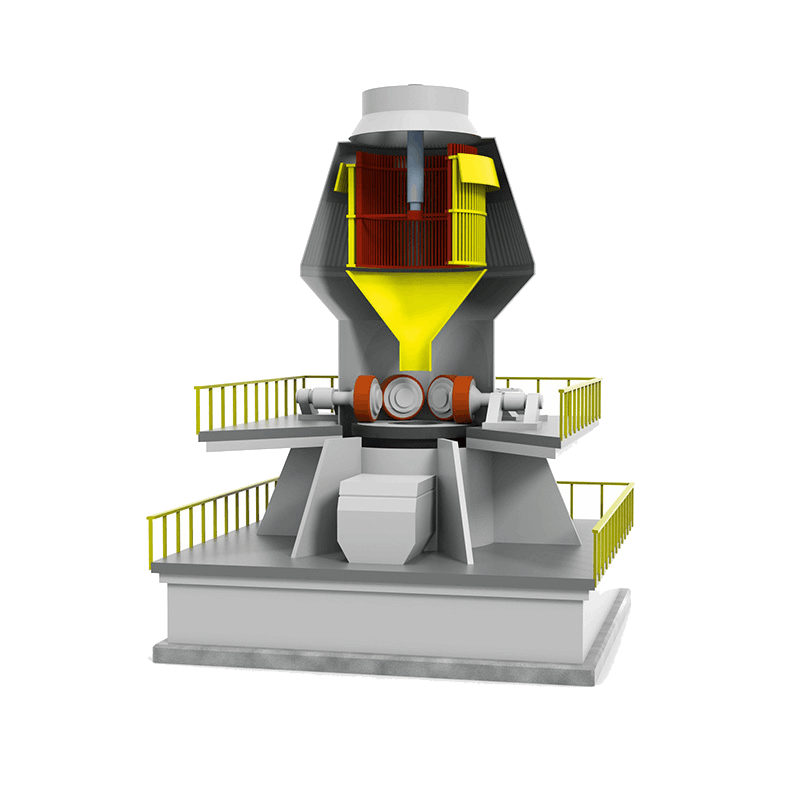
Inside the vertical roller mill
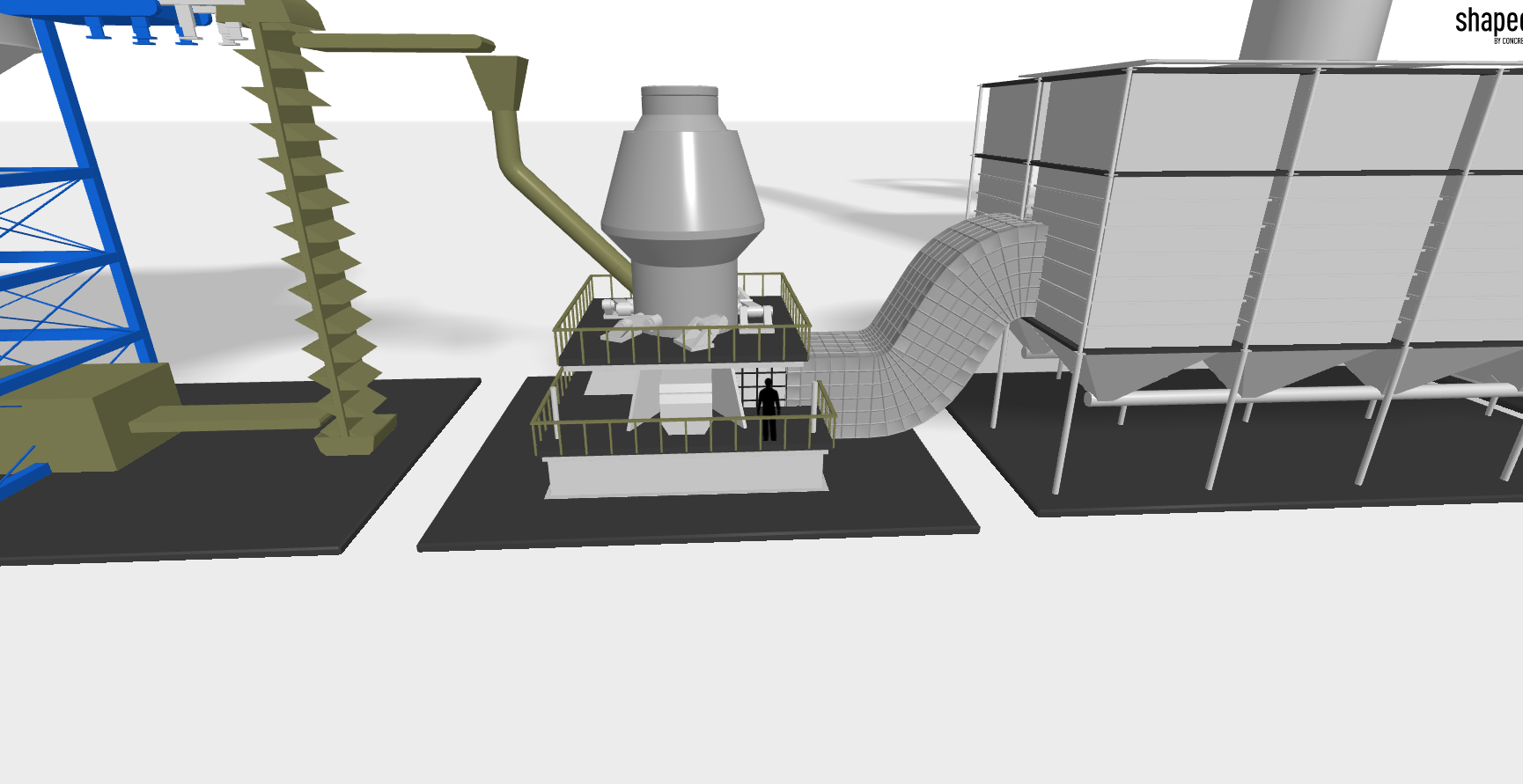
The preheater tower
The material then moves through the preheater tower, starting at the top and moving to the bottom. The pre-heater tower helps make the kiln process more efficient by adding heat generated from the plant to the raw materials, starting the chemical reaction.
Doing this makes the cement process more efficient. Cement production is one of the most efficient in heavy industry, at approximately 80% – for comparison, a typical car runs at about 20% efficiency.
Promising innovations have been developed over the years, such as carbon capture and storage technology, which are being evaluated and can help cement plants reduce their overall carbon footprint.
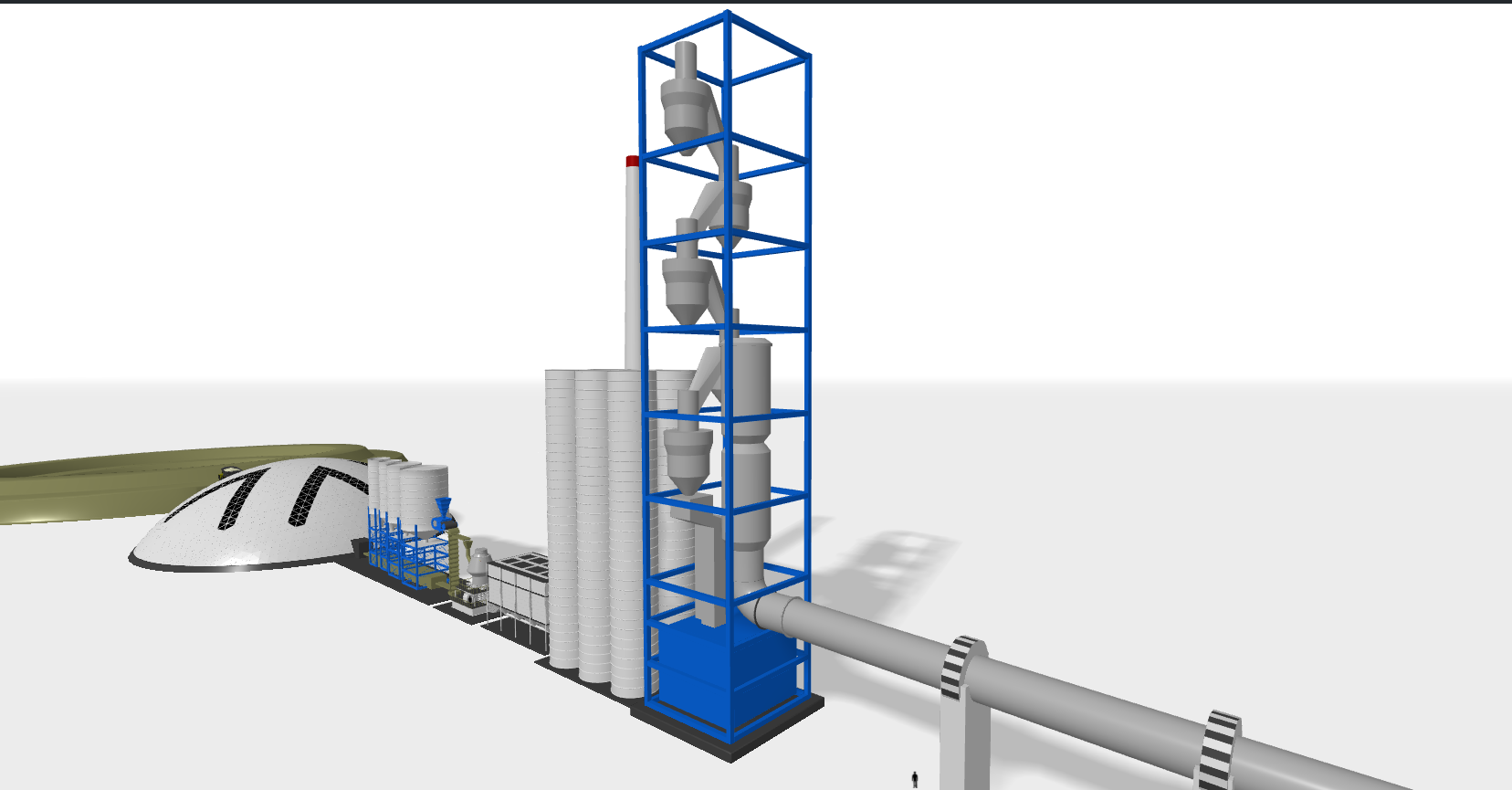
The materials enter the kiln
The cement kiln heats all the ingredients to about 2,700 degrees Fahrenheit in huge cylindrical steel rotary kilns lined with special firebrick and the material becomes partially molten. The finely ground raw material is fed into the higher end of the cement kiln. At the lower end is a roaring blast of flame, produced by the precisely controlled burning of powdered coal, oil, alternative fuels (such as scrap vehicle tires, for example), or natural gas under forced draft. During this process, cement manufacturers have been a leader in the use of alternative fuels to reduce waste going to landfills. In fact, alternatives fuels now represent more than 15% of total cement plant energy consumption in the U.S.
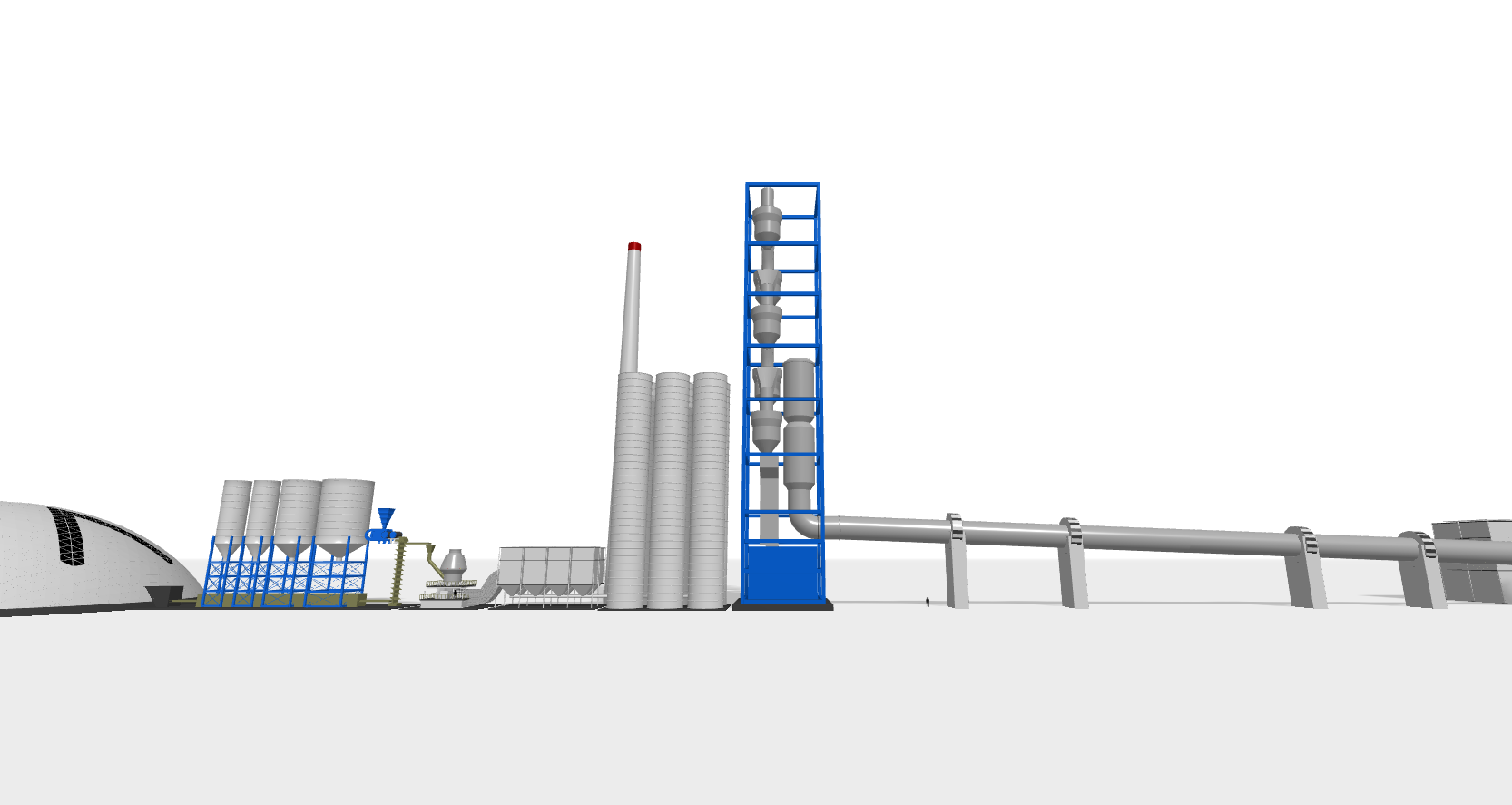
The formation of clinker
As materials move through the kiln, certain elements are driven off in the form of gases. The remaining elements chemically unite to form a new substance called clinker, which comes out of the kiln as grey balls about the size of marbles.
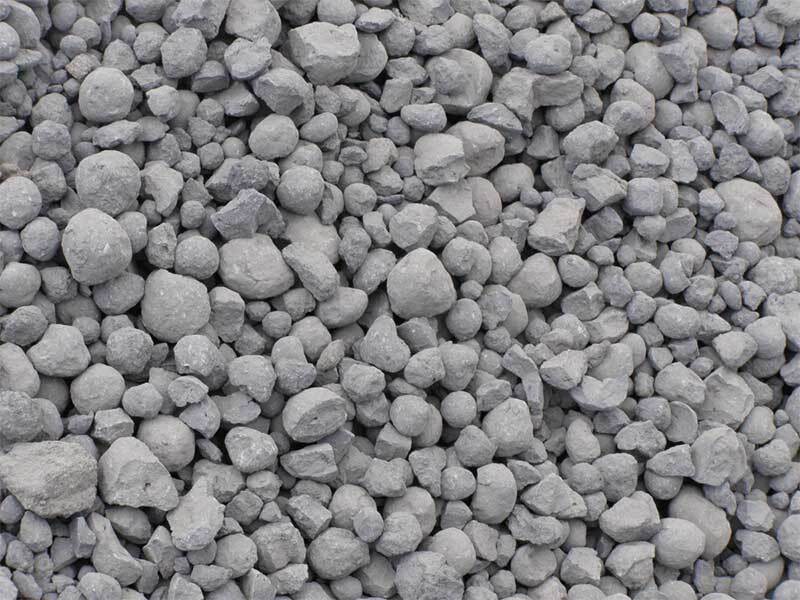
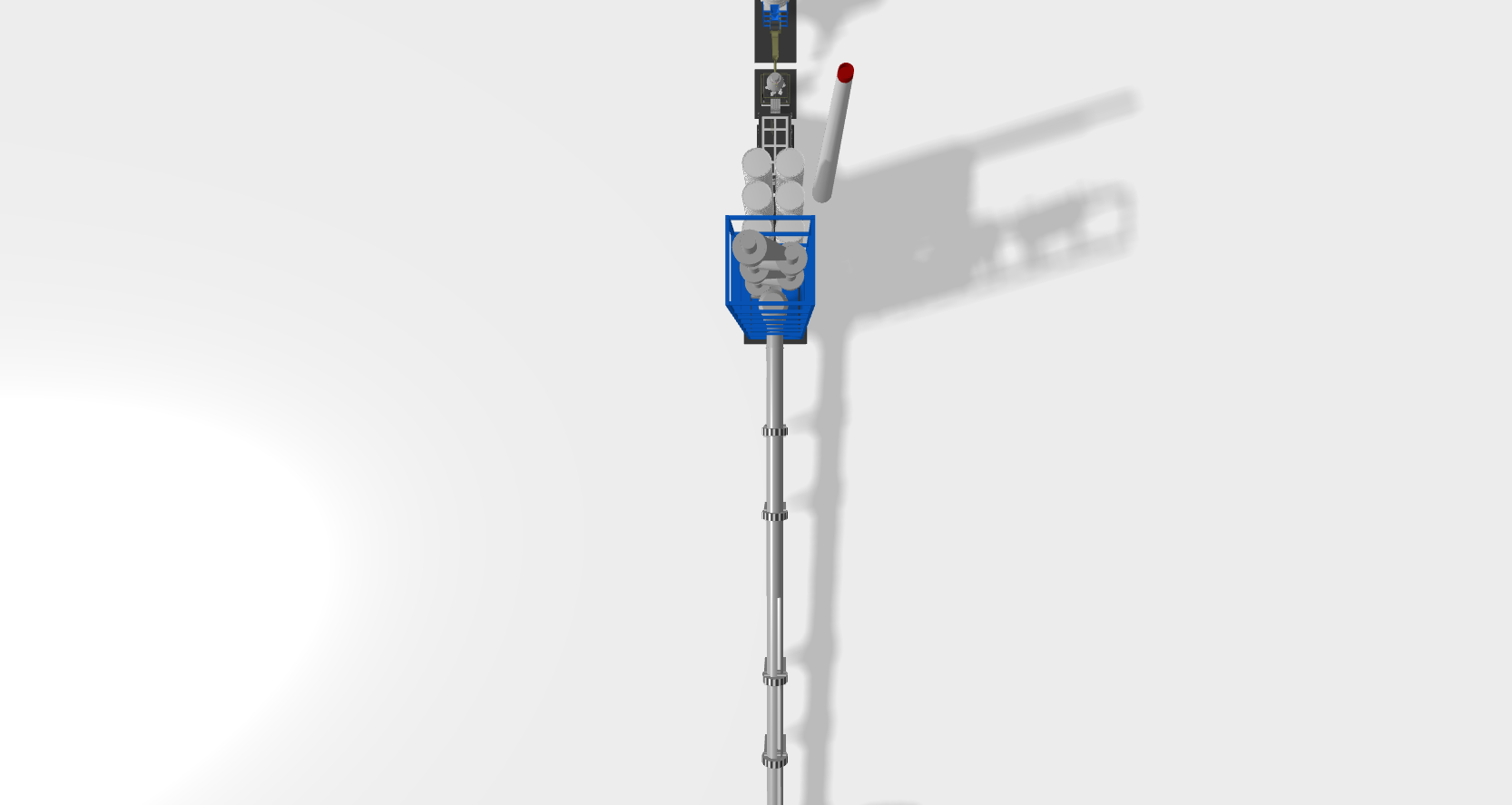
The clinker is cooled for use
The clinker comes out of the kiln red-hot and has a consistency similar to a lava flow. It is brought down to handling temperature in a clinker cooler. Heated air from the coolers is returned to the kilns, a process that saves fuel and increases efficiency.
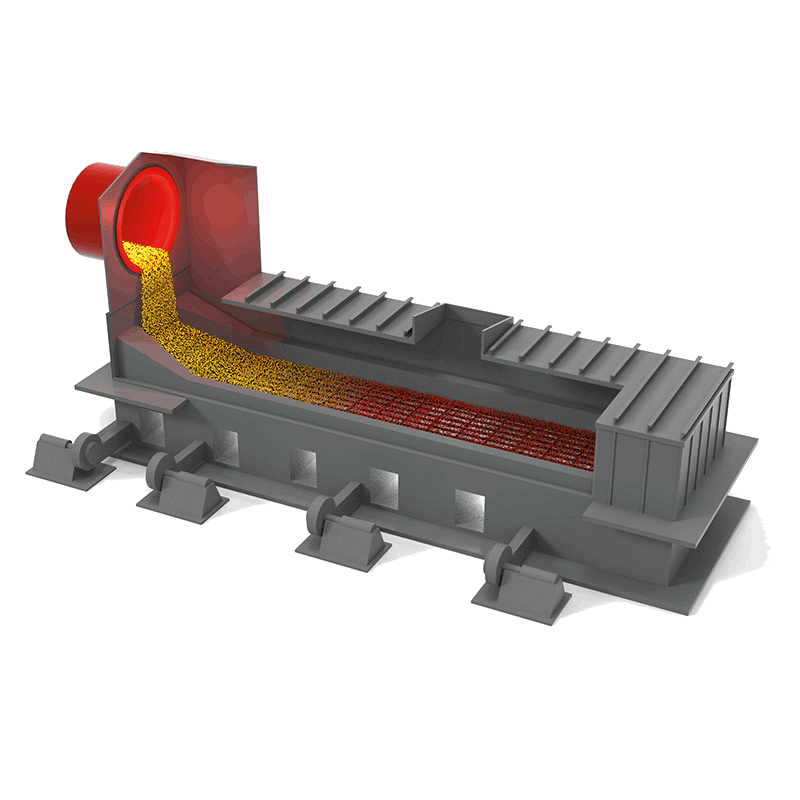
Inside the clinker cooler
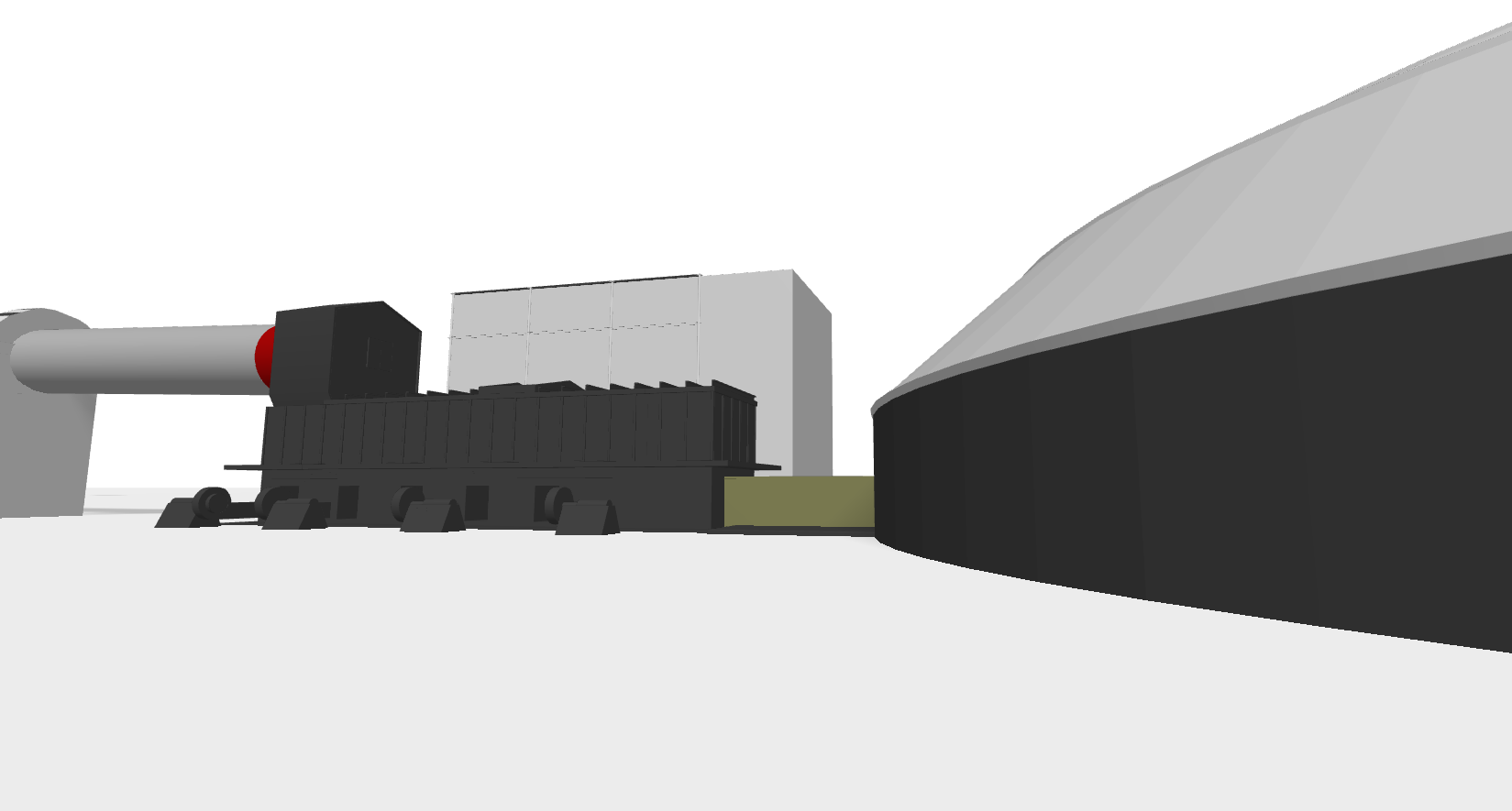
The bag house
Emission control devices exist throughout the process – these are called bag houses. Bag houses collect dust particles and other emissions.
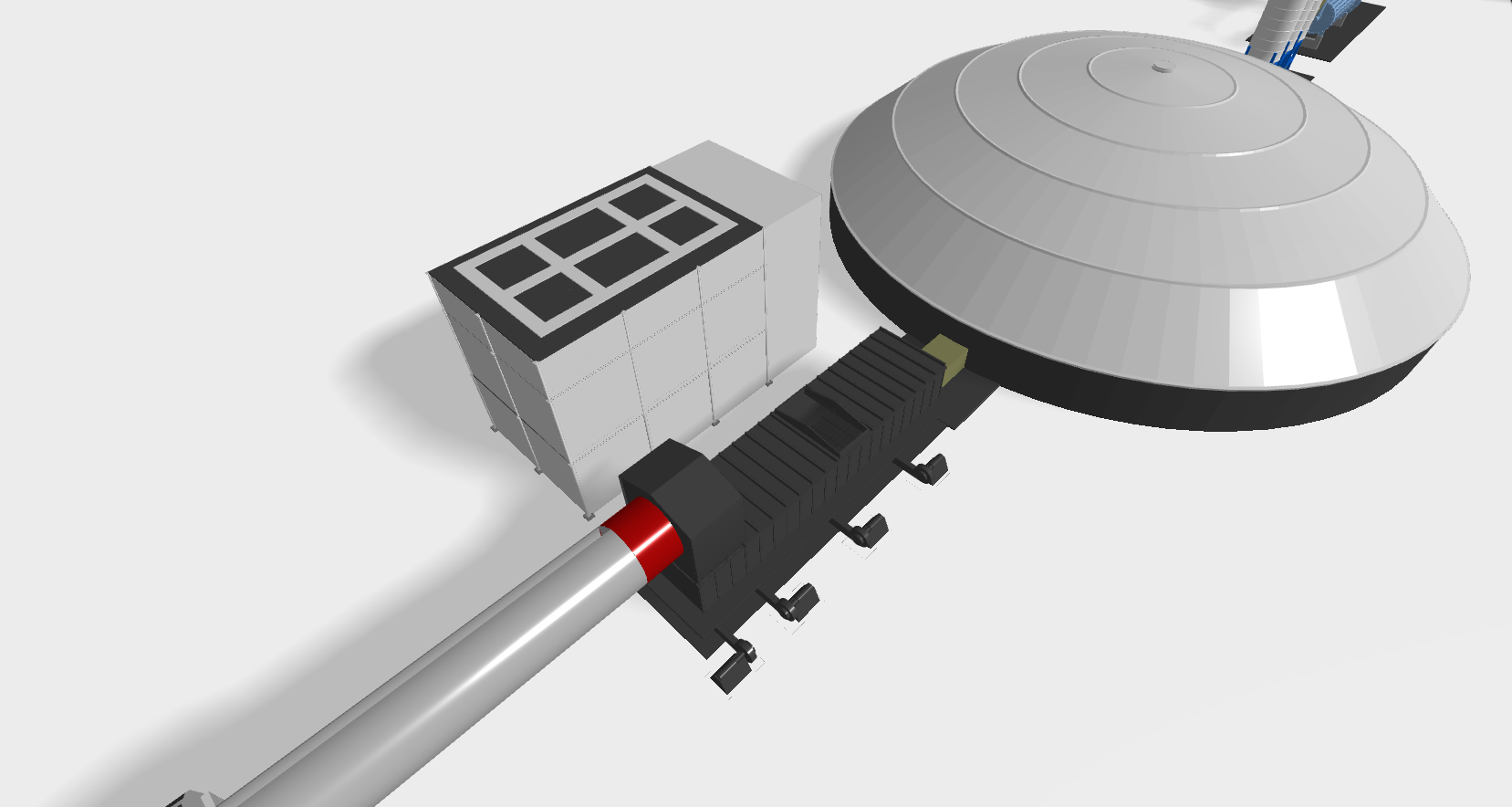
The ball mill
After the clinker is cooled, it is ground with small amounts of gypsum, limestone, and other ingredients to make cement. In this case a ball mill with steel balls is used to reach the fineness needed to achieve desired properties. To reduce the carbon footprint by an additional 10% or more, higher limestone contents or SCMs can be blended in. This permits cements and concrete to achieve the same levels of strength, resiliency, and durability.
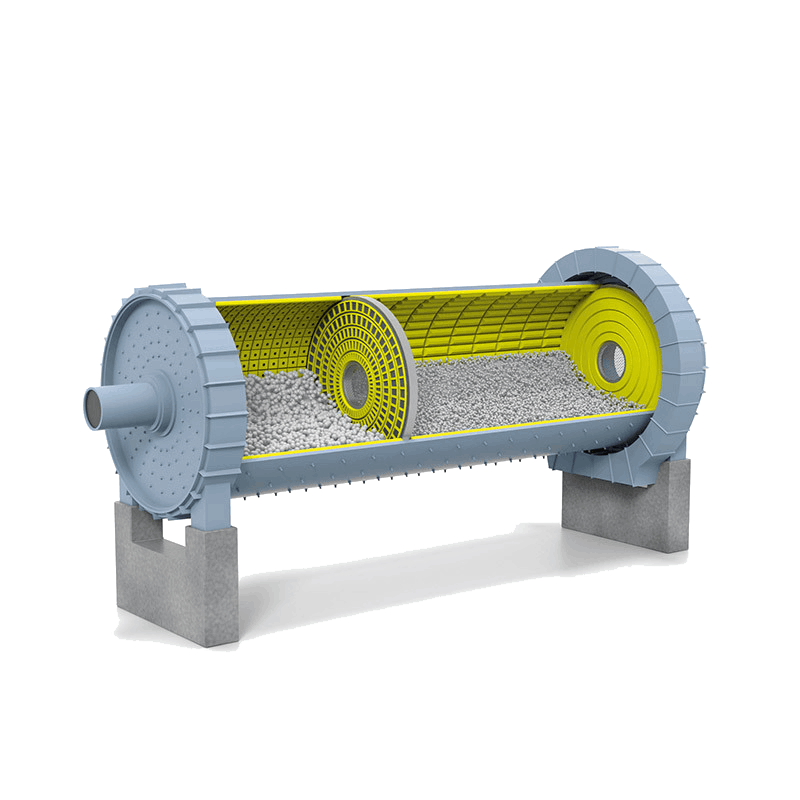
Inside the ball mill
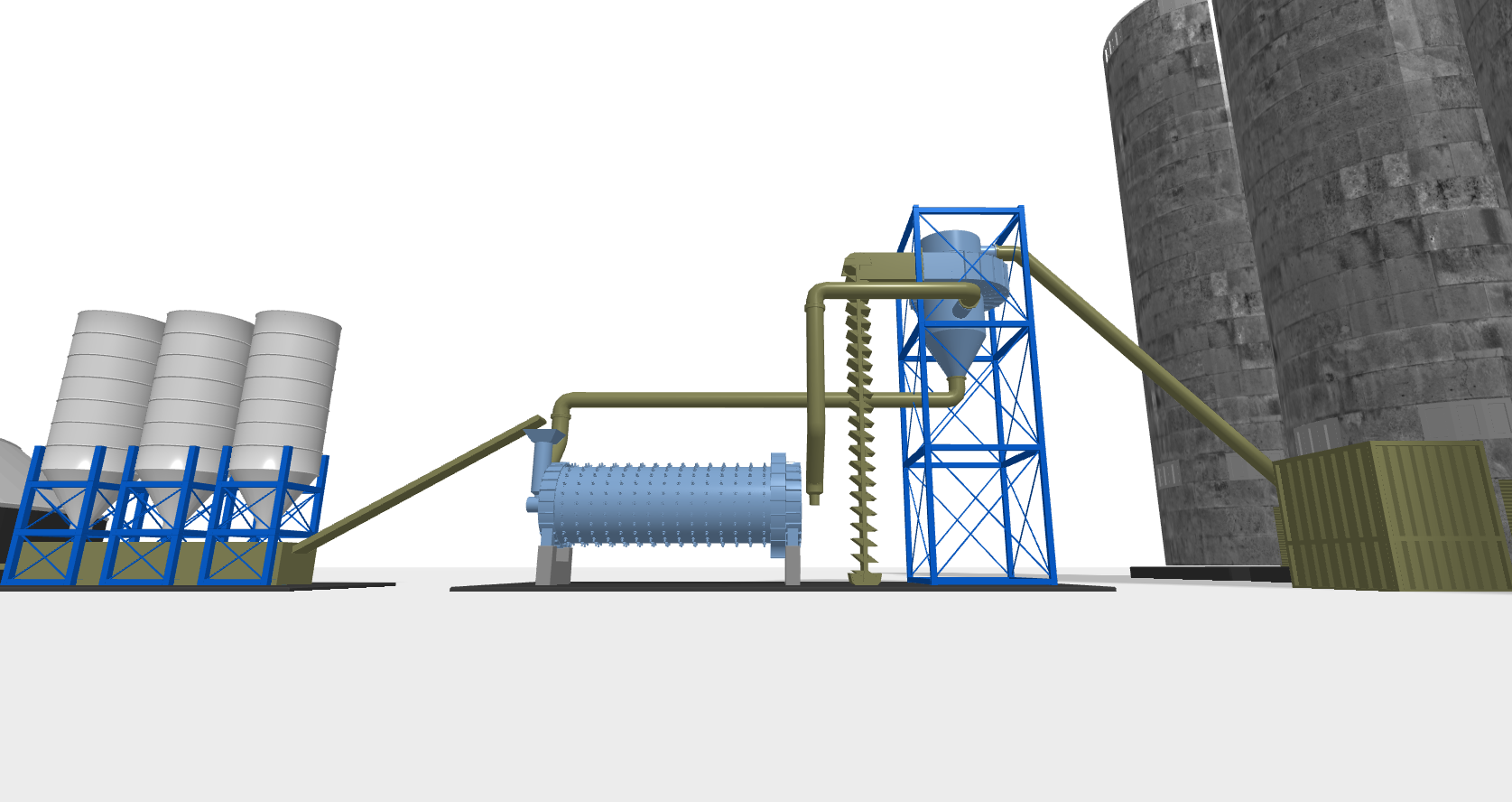
Ready for construction
The cement is ready to be used for construction projects to build long-lasting concrete structures and pavements.
Many construction projects are conveniently located within 15 miles of a ready-mix concrete plant, again limiting energy use and emissions associated with transportation.
Cement is the main ingredient in concrete. Concrete pound for pound is a low carbon footprint material, lower than wood, steel, plastic, or asphalt.
As a versatile and durable material, it is the most widely produced material on earth, providing housing, transportation, water processing and storage facilities, hospitals, and schools. It is a foundational material for modern civilization.
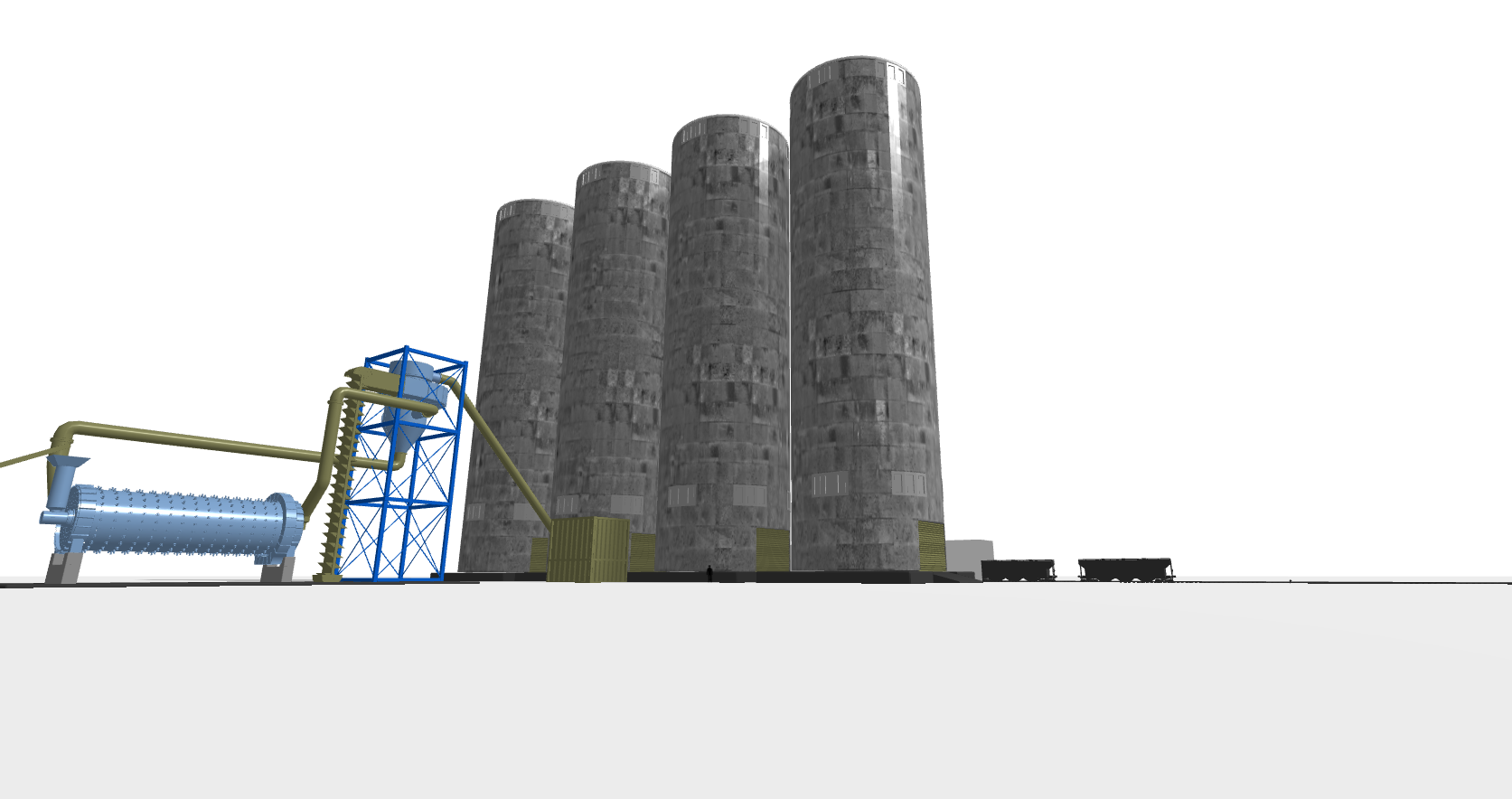